Additive manufacturing applications in the automotive industry are focused on tooling and improving the flexibility of production lines. Our 3D printing software offers automotive manufacturers considerable savings and numerous benefits.


Built with automotive in mind





Thermal simulation and optimisation in Aibuild ensures your inter-layer bonding strength is as great as possible, according to the characterised processing properties of your selected material.

Hard definition of deposition rates in Aibuild means you can guarantee your deposition head is being used to its full potential to put down as fast as possible in the right place.

Carbon fibre SMC parts produced from 3D printed moulds at 6 Bar, allowing for 1.6mm laminates from a single ply.

Custom printing strategies can be defined parametrically and applied to a new CAD in a single click.
Features and Benefits
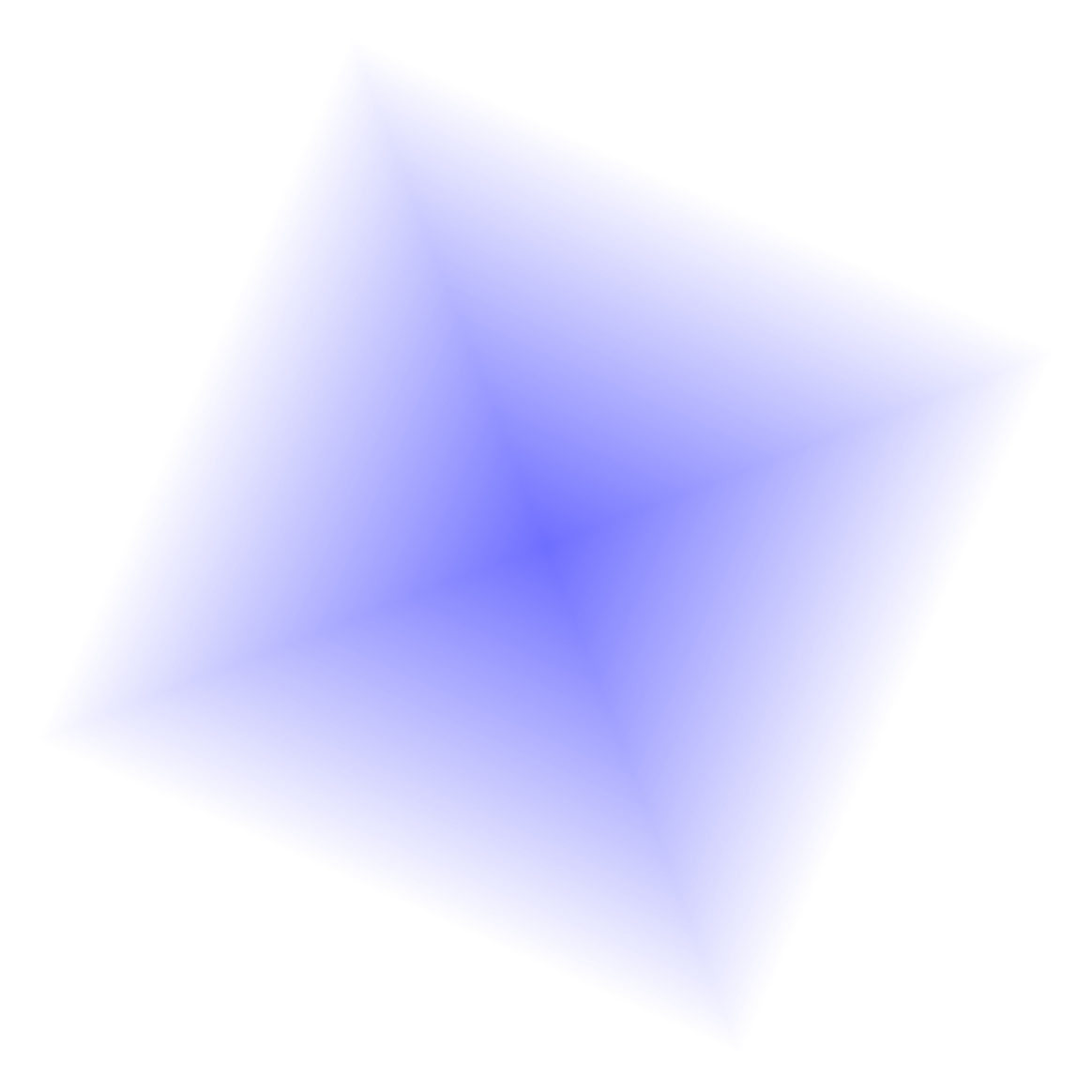
FAQs
Why is Aibuild the best AM technology partner for automotive?
Aibuild has significant experience in addressing the AM requirements of automotive companies from OEM’s to those that are part of the Automotive supply chain. Our software platform’s ability to manage complex geometries and monitor the production process providing real time monitoring and analytics is uniquely placed to meet the demanding needs of the automotive sector from R&D through to production of tooling and end use parts. Today we have tier 1 OEM clients in both Europe and North America.
What manufacturing processes are supported in your software?
Bring your hardware, printers and processes under one roof. Our platform supports a variety of AM processes, including but not limited to:
Polymer pellet extrusion (also known as FGF)
Polymer filament extrusion (also known as FFF)
Metal wire extrusion (also known as DED, direct energy deposition)
Metal wire arc (also known as WAAM)
Concrete
Ceramic
Other additive processes
Subtractive processes (e.g. milling for finishing)
Is LFAM ready for production? Is it still in a research-stage?
Multiple OEMs and Tier 1s in various industries are using LFAM to make production parts today.
How do you connect AM hardware, software and materials?
The software platform is a central hub for various AM data inputs, including materials data, hardware configuration, as well as process steps and parameters. Our extensive partner network helps us to maintain an up-to-date library of printers and material data. Our lab’s additional material testing, research studies and testing helps us to tailor recommended settings and our algorithms to ensure you get the best quality without having to go through various trial-and-error iterations to get a good quality print.
How can you ensure zero-changes to my part over the course of a typical automotive product lifecycle?
All workflows from June 2024 onwards are fully backwards compatible. This means your sliced parts & toolpaths aren’t affected by new updates to the platform. You have the choice to upgrade your projects to the latest version, or to continue to use the version that you used to generate your toolpath. You can make edits, add new process steps, re-compute, change input files and more, even though you aren’t using the latest version of the software. A toolpath made in 2024 and be edited and re-computed in 2034. This ensures repeatability and traceability across the full automotive product development cycle, from design to prototyping to manufacture and inspection. This is the power and flexibility of the cloud.
Do automotive companies use your software?
Yes, we currently have both OEM’s and supply chain customers using Aibuilds software platform every day, in both R&D and production of tooling components and end use parts in various materials and on various hardware systems
Contact us