Additive manufacturing is playing a pivotal role in shaping the future of the aerospace, space and defence industries. We serve these sensitive applications with a 3D printing platform that protects your vital data.


Built with aerospace in mind






Gain manufacturability insights through online control of printers and real-time sensor information, compiled per build.

Path planning optimised to enable large overhangs support-free enables new and more performant parts to be manufactured.

FST compliant materials characterised in Aibuild, including ULTEM 1010, unlocking LFAM applications in aircraft interiors.

Securely share files, workflows and manufacturing data across your organisation within Aibuild. Aibuild meets the highest ISO standards for data security, as well as offering solutions within AWS govcloud and on-premise.,

Aibuild enables secure remote control of printers, enabling remote machine operators to remotely execute builds for in-field repairs and replacements.
Features and Benefits
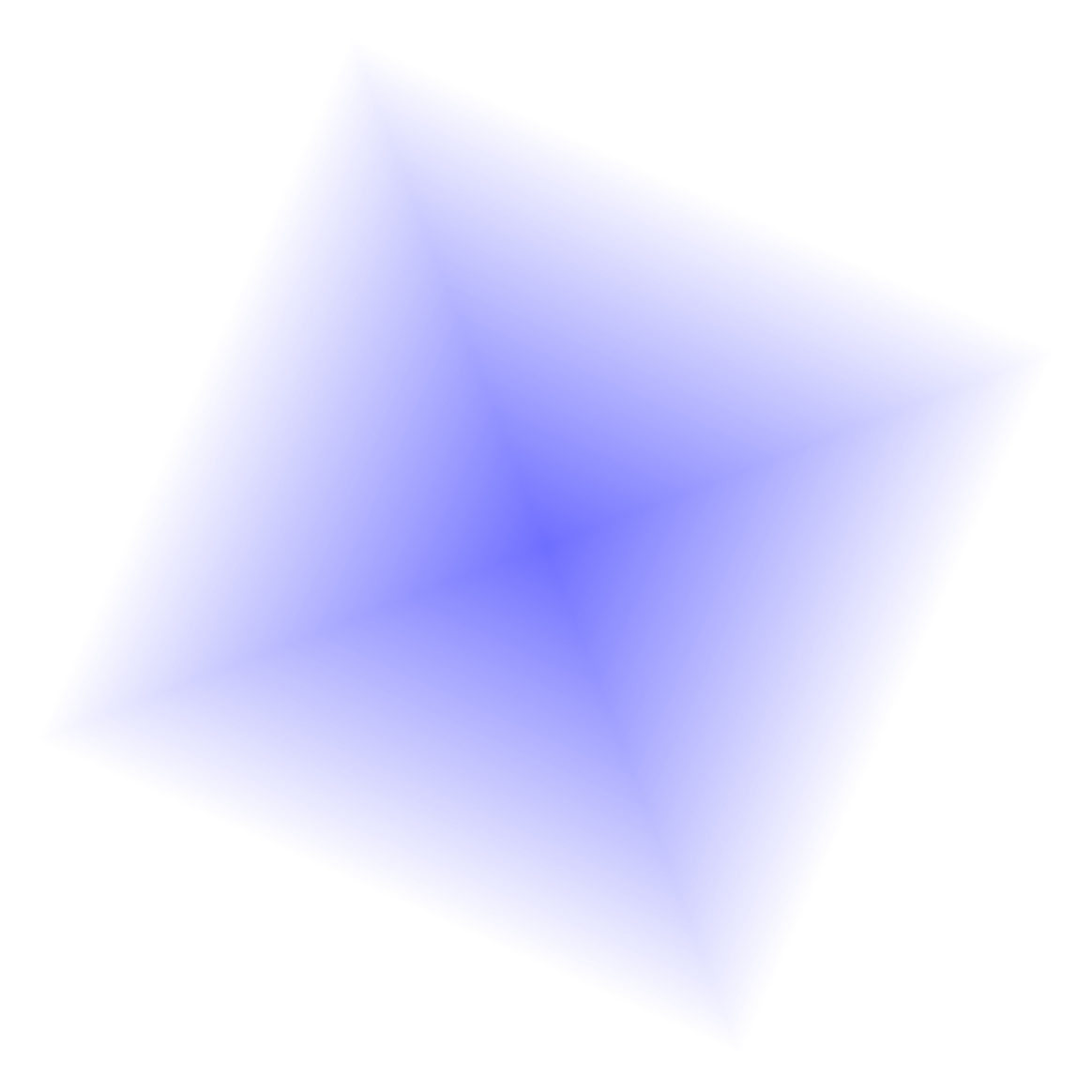
FAQs
What manufacturing processes are supported in your software?
Bring your hardware, printers and processes under one roof. Our platform supports a variety of AM processes, including but not limited to:
• Polymer pellet extrusion (also known as FGF)
• Polymer filament extrusion (also known as FFF)
• Metal wire extrusion (also known as DED, direct energy deposition)
• Metal wire arc (also known as WAAM)
• Concrete
• Ceramic
• Other additive processes
• Subtractive processes (e.g. milling for finishing)
How do you connect AM hardware, software and materials?
The software platform is a central hub for various AM data inputs, including materials data, hardware configuration, as well as process steps and parameters. Our extensive partner network helps us to maintain an up-to-date library of printers and material data. Our lab’s additional material testing, research studies and testing helps us to tailor recommended settings and our algorithms to ensure you get the best quality without having to go through various trial-and-error iterations to get a good quality print.
How is this different from a standard slicer?
Traditional 3D slicing software does not have the ability to do robot programming or simulate the motion of a robotic or gantry system. They allow generation of machine instructions, but these are generic G-code and often post-processing is required to translate these instructions to a language your specific machine, controller and configuration can understand and use to print a high-quality part.
For large-format additive manufacturing, there are additional complexities. Due to the larger part sizes, a higher deposition rate (kilogram-per-hour) is generally required. This often means printing with a larger “bead” (line of extruded material) which can lead to is thermal build up in the core of the extruded material. Temperature is key in additive manufacturing to achieve good bed adhesion and interlayer bonding to prevent thermomechanical defects such as sagging. Aibuild has been built to solve these particular challenges.
Multi-axis printing with robotic systems offers you the ability to print without supports and to print complex structures in much less time and with less post-processing of the part which standard slicing software does not offer. This generally means a user would need to pair a standard slicer with a robotic programming software tool to achieve a similar result.
How is this different from robotic programming software?
Offline robotic programming software does not take the manufacturing process into consideration. It is a solution for pure kinematic control of the machinery without an understanding of the part, geometry, extrusion process, material, quality issues and more. Aibuild software is built to tackle AM, LFAM and robotic AM head on.
What methods do you use to ensure security on the platform?
We understand the security and data control requirements in the aerospace industry. You can enable multi-factor authentication (2FA) to ensure extra security to access your account. This can be enforced per user or at an account-level if it is mandatory by your IT team. We are ISO 27001 certified, ITAR compliant and have solutions for high-security applications if these are required by your organisation.
How can you ensure zero-changes to my part over the course of a typical aerospace product development cycle?
All workflows from June 2024 onwards are fully backwards compatible. This means your sliced parts & toolpaths aren’t affected by new updates to the platform. You have the choice to upgrade your projects to the latest version, or to continue to use the version that you used to generate your toolpath. You can make edits, add new process steps, re-compute, change input files and more, even though you aren’t using the latest version of the software. A toolpath made in 2024 and be edited and re-computed in 2034. This ensures repeatability and traceability across the full aerospace product lifecycle, from design to prototyping to manufacture and inspection. This is the power and flexibility of the cloud.
How are you using artificial intelligence (ai) in your software?
A number of challenges in additive manufacturing lend themselves to large language models and machine learning. Artificial intelligence (AI) is a tool we use to address the knowledge gap for newcomers to get started, and to solve challenges that intermediate users and experts face. It is deployed in the product today via our recommendation engine, that recommends the next command based on the workflow you are building, our GPT-style text interface, where you can prompt the software to follow a manufacturing process, our defect detection monitoring algorithm* that can identify quality issues in a build, as well as other areas we’re excited to talk about in the near future! (*hardware-dependent).